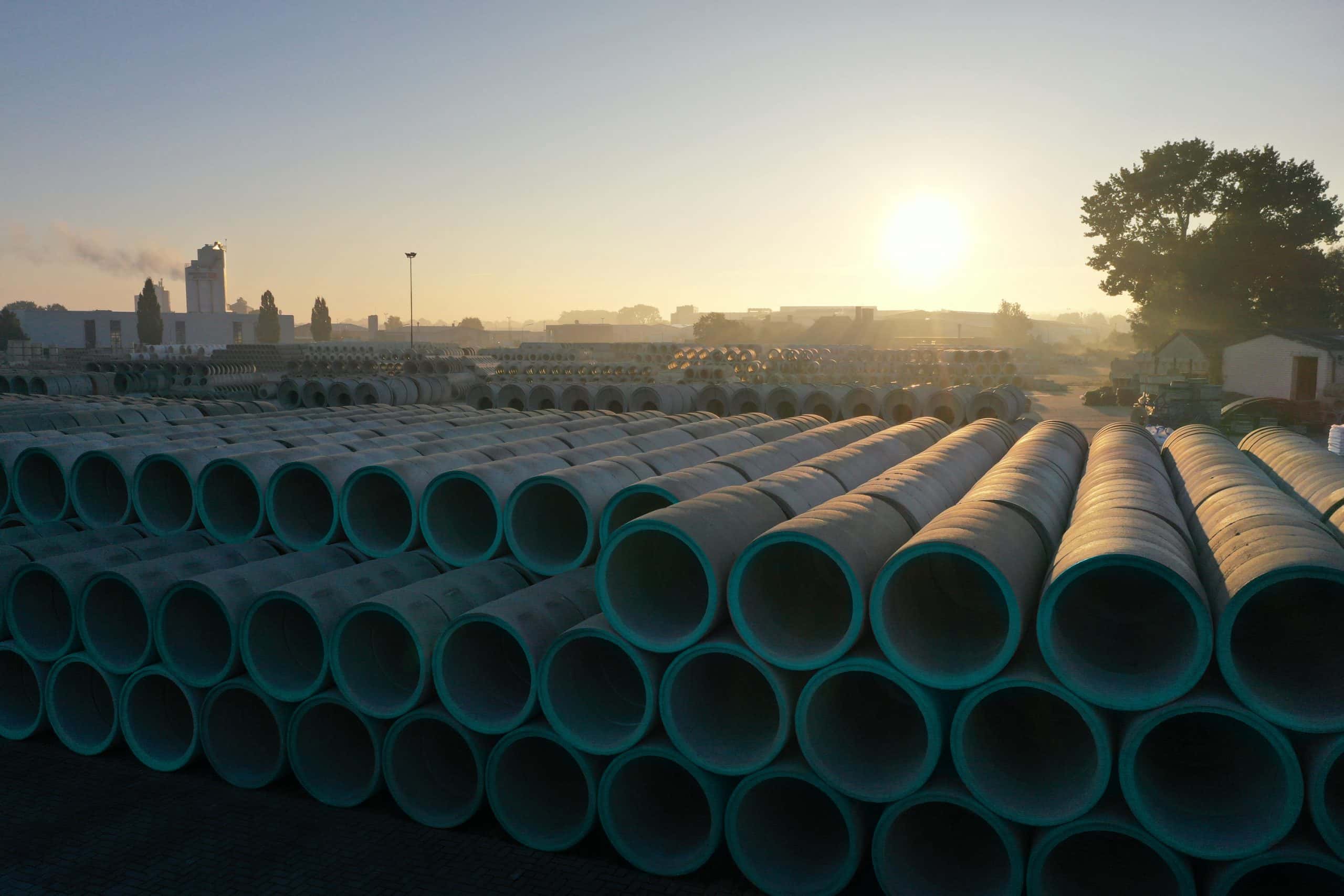
GEOPOLYMERBETON:
BEWÄHRTE TECHNIK NEU ENTDECKT
next.beton – zementfrei klimafreundlich
GEOPOLYMERE – URSPRUNG UND ENTWICKLUNG
Die ersten wissenschaftlichen Veröffentlichungen zum Thema Geopolymere erschienen bereits in den 1970er Jahren. Schon Jahrzehnte zuvor wurden alkalisch aktivierte Tone, Aschen oder Schlacken als latent hydraulische Bindemittel untersucht. Zu einem ersten industriellen Einsatz von Geopolymeren kam es in Osteuropa und Russland. Hier wurden Geopolymere u.a. zur Herstellung von Bahnschwellen verwendet. In größerem Umfang wurden Geopolymere zum ersten Mal in den 1990er Jahren durch den amerikanischen Zementhersteller Lone Star Industries genutzt. Dieser setzte eine Mischung aus Zement und Geopolymer im Tief- und Straßenbau ein.
Den Durchbruch im Bereich Geopolymerbeton erreichte jedoch 2004 das australische Unternehmen Wagners mit der Entwicklung von EFC® (Earth Friendly Concrete®).

EFC® (Earth Friendly Concrete®)
DER DURCHBRUCH IM BEREICH GEOPOLYMERBETON
Zur Herstellung von EFC® wird ein Geopolymer-Bindemittel verwendet, das aus der chemischen Aktivierung von zwei Industrienebenprodukten (zum Beispiel Hochofenschlacke und Flugasche) entsteht. Die umweltfreundliche Betontechnologie bietet ein erhebliches CO2-Einsparpotenzial, ohne dabei die technischen und konstruktiven Qualitäten von Beton zu vermindern.
Eine besondere Eigenschaft des Geopolymerbetons ist seine Widerstandsfähigkeit gegen chemische Angriffe.
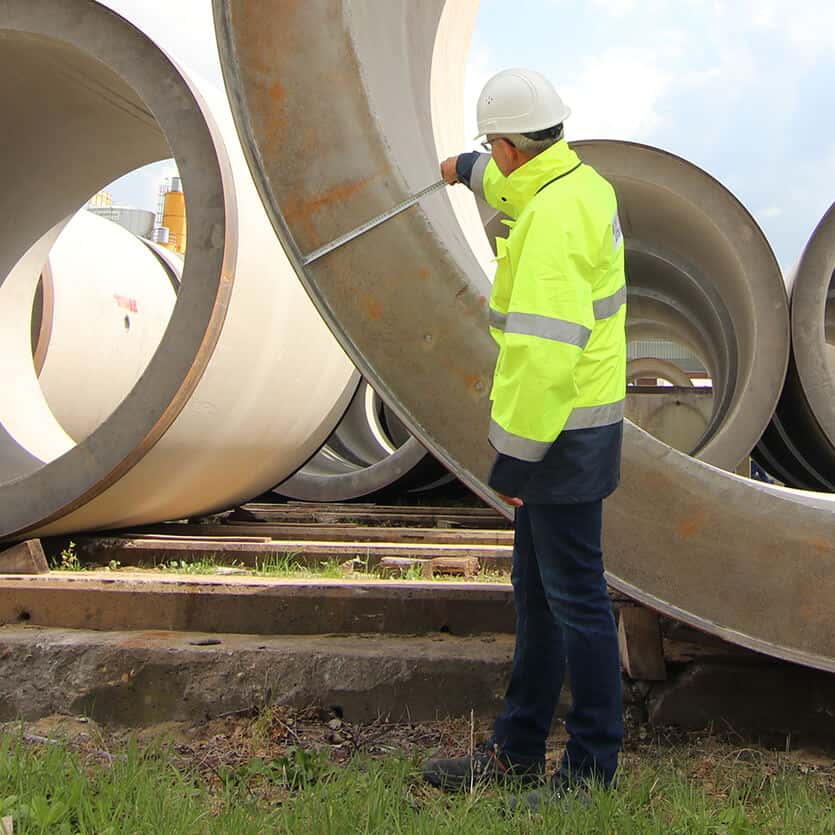

MIT EFC® ZU NEXT.BETON – DEM KLIMAFREUNDLICHSTEN KANALSYSTEM DEUTSCHLANDS
2011
UNABHÄNGIGER INGENIEURBERICHT,
der die gleiche oder bessere Leistung als herkömmlicher Beton gemäß den Leistungsanforderungen des australischen Standards AS 3600 „Concrete Structures“ zeigt.
2012
BETEILIGUNG AM BAU DES GLOBAL CHANGE INSTITUTE
5-stöckiges Mehrfamilienhaus an der Universität von Queensland. Eine weltweit erste Anwendung von modernem Geopolymerbeton in einem tragenden Element eines mehrstöckigen Gebäudes.
2013
EFC® ERHÄLT DEN BPN SUSTAINABILITY AWARD
2014
FLUGHAFEN BRISBANE WESTWELLCAMP
51.000 m² Schwerlastbeläge aus EFC® für Wendeknoten und Rollbahnbereiche. EFC®-Beton wurde auch für die Fundamente und Wandplatten des Terminalgebäudes und alle Bauarbeiten auf dem Gelände, einschließlich der Eingangsbrücke, geliefert. Allein bei diesem Projekt wurden rund 8.800 Tonnen CO₂-Emissionen durch die Verwendung von EFC® eingespart.
2015
QUEENSLAND STATE AWARD FOR EXCELLENCE – „ENGINEERING PROJECTS“
verliehen vom Concrete Institute of Australia (CIA)
2015
CIA NATIONAL SUSTAINABILITY AWARD – SEHR EMPFEHLENSWERT
2016
EFC® ERHÄLT DIE ACI AUSZEICHNUNG
American Concrete Institute (ACI) Global Excellence in Concrete Awards Winner – Flatwork category
Dezember 2020
PRODUKTION DER ERSTEN EFC® STAHLBETONROHRE
Nachdem Günter Röser auf EFC® aufmerksam geworden war, setzten er und seine Söhne Carl Maximilian und Louis Röser sich das gemeinsame Ziel, klimafreundliche Betonkanalsysteme auf EFC®-Basis herzustellen, die jede Kommune und jeden Planer in Deutschland in die Lage versetzen sollte, ein über die gesamte Lebensphase hinweg nachhaltiges Kanalsystem zu realisieren. Um dieses Ziel zu erreichen, setzte die Röser Unternehmensgruppe, die mit ihren Werken flächendeckend Süddeutschland beliefern kann, auf eine Partnerschaft mit BERDING BETON GmbH und der Finger Baustoffe GmbH.
April 2021
STARTSCHUSS FÜR NEXT.BETON – ZUSAMMENARBEIT DER DREI BETONSPEZIALISTEN
Durch die Zusammenarbeit der Röser Unternehmensgruppe, von BERDING BETON und Finger Baustoffe ist sichergestellt, dass die Transportwege der Rohstoffe sowie die Wege der Produkte zu den Kunden kurz gehalten werden können und Planer und Kommunen im gesamten Bundesgebiet Zugriff auf das neue next.beton Kanalsystem erhalten. Zudem kooperieren die Unternehmen im Zusammenhang mit der Erlangung der DIBt-Zulassung und im Marketing, agieren darüber hinaus jedoch wirtschaftlich und vertrieblich vollständig unabhängig voneinander.
November 2021
EINREICHEN DER PRODUKTIONSDATEN UND MUSTERSTÜCKE BEIM DIBT
Mai 2022
OFFIZIELLE VORSTELLUNG DES NEXT.BETON KANALSYSTEMS AUF DER IFAT IN MÜNCHEN
Mai 2024
Erfolgreiche DIBt-Zulassung
DIE VORTEILE VON NEXT.BETON AUF EINEN BLICK
UMWELTFREUNDLICHKEIT
Massive CO2-Einsparungen
Durch den Einsatz eines zementfreien Bindemittels können bei der Herstellung von next.beton bis zu 70 Prozent der CO2-Emissionen eingespart werden.
INNOVATIVE FORMULIERUNG
Zementfreier Beton
Bei der Produktion von next.beton wird der energieintensive Zement durch ein Geopolymer-Bindemittel ersetzt – völlig ohne technische oder qualitative Einbußen.
XA3-KOMPETENZ
Hohe Säure- und Sulfatbeständigkeit
Wegen seiner kalkfreien Zusammensetzung ist next.beton für XA3-Anwendungen ohne aufwendige Zusätze, Beschichtungen oder Einbauten einsetzbar.